
The paper industry is working hard to build a completely waste-free factory in the future and offer solutions to save forest resources. One solution is to reuse white water in the production line. So, what are the problems arising from the reuse of white water in paper and board production? All will be in our detailed article below.
White water in the papermaking industry is the water that comes out after the powder concentration process and is released in the paper-making process, the meshing and pressing stages. The composition of the white water depends on the machine type, the type of pulp, the type of non-fibrous additive and the number of vacuum boxes in the wet part of the machine. Basically, white water contains short fibers, soluble substances and a large percentage of additives such as fillers, starches, colors, etc.
The problems arising from the reuse of white water in paper and board production are listed in the table below. They can be divided into three categories: high levels of suspended solids; accumulation of dissolved solids; and increase in heat conservation.
Increase in suspended solids | Increase dissolved solids | Increase heat energy |
DustAbrasionSmall seedtarpaulin, netTime to use tarpaulinSurfing usage timeDrainage rate is reducedPlug into the spray | Dilute mudFoamCorrosiveGlueSpeckles on paperColorpH controlPrecipitationDepositionOdorTime saved | TemperatureGlue problemMachine room temperatureVacuum pump capacity reduced |
Solubilizers and colloids cause more serious problems than suspended solids. After a long period of operation with reduced clean water costs, there will be scaling and equipment corrosion. The high level of water circulation leads to an increase in the concentration of solutes to the extent that it affects the additive process (glue, foam, …) and machine operation, increases the content of short fibers in the paper … In many cases reuse of white water increases drainage by increasing white water temperature.
1. The problem of clogging the mesh washing system
The most common problem when reusing white water is the blockage of the net spray system, tarpaulin and spray in the locomotive box. The main cause is due to the presence of long fibers (usually greater than 3mm) in the white water. To overcome this phenomenon, it is possible to use sieves with grooves smaller than 5-7 times the fiber length to be removed. For example, if the mesh nozzle diameter is 0.13 – 0.15 mm, use sieve #60. This sieve is also used to remove the residue in the clean water supplied to the nozzle.
2. Corrosion
The system can be corroded by electrochemistry and by microorganisms. Corrosion rate is affected by a series of interacting factors such as: dissolved oxygen level; pH; dissolved solids; chloride; sulphate; …hardness of water; alkalinity; acidity; temperature; speed of flow through the surface; carbon dioxide concentration; and contact with other metals. The many factors involved in the corrosion process make it complex and difficult to control.
Corrosion reduces equipment life and increases maintenance costs. However, these effects over time are difficult to determine because the rotation of the device changes. To solve this problem requires improvement, but this will increase equipment maintenance costs. In some thin paper factories, equipment made from other materials has been removed from the system, or insulated with adjacent equipment. Most corroded steel pipes are replaced by stainless steel pipes or fiberglass pipes.
Techniques that allow for corrosion control include pH adjustment, cathodic protection, protective coating and the addition of chemical inhibitors. Possible inhibitors are calcium bicarbonate, chromate and dichromate, nitrates, polyphosphates, silicates, borates, sodium benzoate and organic inhibitors. There is no universal inhibitor for white water. The most promising substances are polyphosphates, silicates and borates. So far, however, chemical inhibitors have not been used in the water system of the paper mill.
In aerobic conditions electrochemical corrosion tends to predominate, but in anaerobic conditions microbial corrosion becomes important. The presence of sulfates that accumulate during the reuse of white water and sulfate-reducing bacteria accelerates corrosion. The product of sulphate reduction is the odorous sulfide. Corrosion by microorganisms can be controlled by the use of biocides. Corrosion rate of about 0.9 mm/year is acceptable, from 0.9 to 1.3 mm is to be considered, and if it is greater, measures to reduce the rate of corrosion must be applied.
3. Mud and smell
Sludge and odor should be considered together because in all cases odor generation is related to biological development. Most odor problems that arise in white water systems are caused by poor management, no effective disinfection program, or stagnant water in the water or in the powder preparation system.
Due to the implementation of reuse of white water in production, the concentration of solutes increases in the system. The increase in carbohydrates and nutrients favors the growth of bacteria. The ability to inhibit bacterial growth in nutrient-rich media is slower and the concentration of biocide added to the system increases. When large amounts of water are reused, the temperature will increase from 20 – 35 °C to above 50 °C, causing a large change in the bacterial population. Thermophilic microorganisms tend to form spores and are therefore difficult to eradicate or control. Operating the plant water system at a temperature high enough to prevent bacterial growth for reasons of human safety and convenience is not feasible.
Plants deal with the sludge problem by doing industrial cleaning more frequently and adding biomass production inhibitors to certain work points in the system. The biocides used are chlorine and derivatives, phenols, organic sulfur compounds and silver compounds.
4. Color
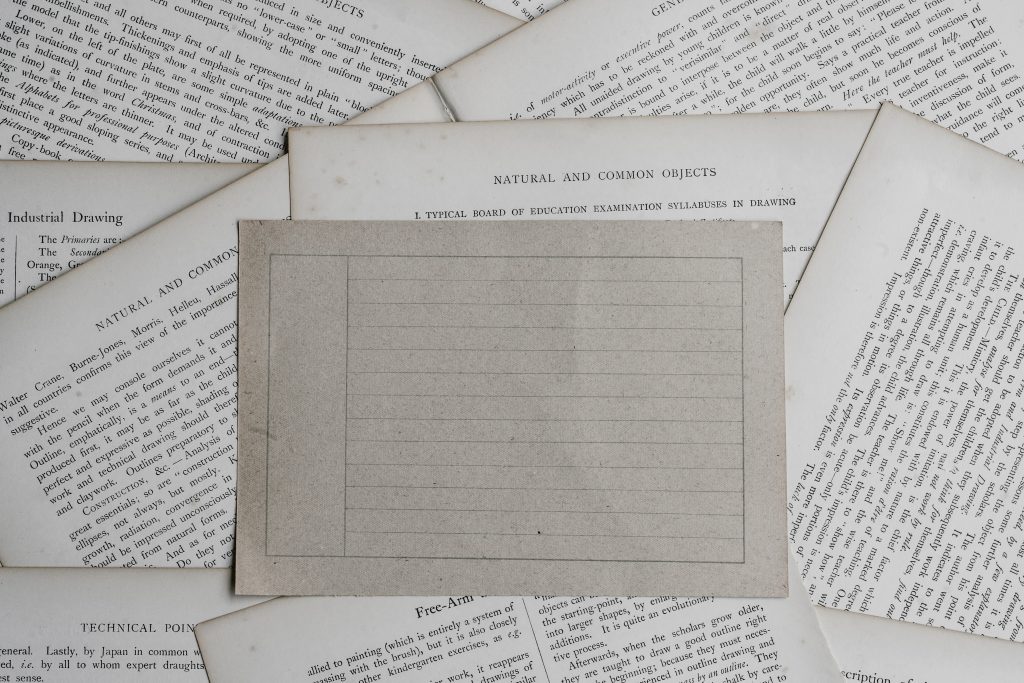
The color of the circulating water is problematic when producing white and colored paper alternately. To overcome, it is recommended to start production with white paper with clean water, run with clean water until the white water is enough to break the powder in hydraulic grinding and adjust the concentration; if the factory produces colored paper then the next production should be lighter colored paper and finish with the darkest colored paper. It is then necessary to clean it thoroughly before starting a new cycle. Water cycling is improved if the dye is well coloured, and easy to remove. The white water system should be separated for efficient reuse in the case of multiple machines producing white and colored paper at the same time.
5. Accumulation of dissolved salts
As the emissions are reduced and the amount of white water circulating in the plant increases, the electrolyte concentration increases significantly. Many processes in the wet part of the machine, especially those that depend on ionic attraction or repulsion, will be altered in such an environment of high salt concentration.
Testing with a fully enclosed machine model at Western Michigan University led to the conclusion that catalog paper can be produced from 70% ground wood pulp and 30% sulfate powder in a fully enclosed condition. It was found that increasing salt concentrations up to 4000 mg/l had little effect on the mechanical and optical properties. Tests confirmed at the University of Michigan produce paper with opacity under the condition of reuse of all white water.
Reference source: Book “Environmental protection in pulp and paper industry” – Author: Doan Thai Hoa – Publishing House: SCIENCE AND TECHNOLOGY
In charge of the article: Do Thi Hue